Top Benefits of Outsourcing Metal Stamping Services for Your Manufacturing Needs
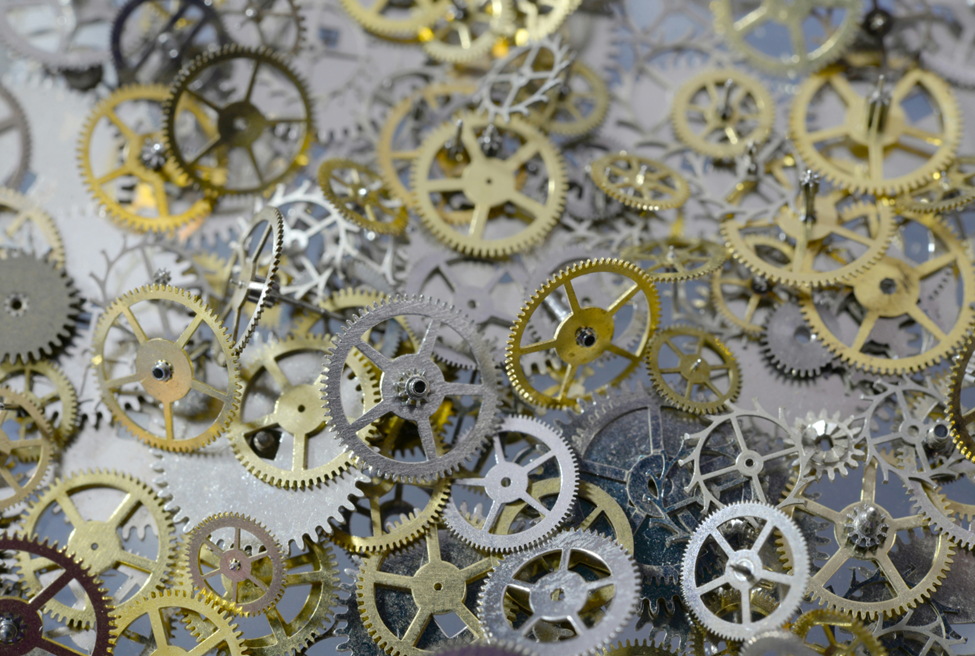
Photo by Laura Ockel on Unsplash
Manufacturing businesses often look for ways to maximize their operations while keeping high standards and efficient cost control. For companies trying to simplify their manufacturing processes, outsourcing specialized manufacturing activities has become a strategic answer. The choice to outsource metal forming and fabrication techniques can greatly affect operational efficiency and bottom-line outcomes for manufacturers needing precise components.
Cost-Effective Production Solutions
Partnering with specialized metal stamping services providers eliminates the need for substantial capital investments in equipment, tooling, and facilities. Purchasing and maintaining stamping machines, dies, precision measuring instruments, and other specialized production equipment may be avoided by your company, saving the significant costs involved. Outsourcing also helps save overhead connected to staff training, quality control systems, facility upkeep, raw material storage, and continuous equipment improvements. By assuming these obligations and related risks, the service provider enables your business to better allocate resources towards core business activities, strategic planning, research and development, and expansion projects while preserving a leaner operational structure and increasing general cost efficiency. Without sacrificing manufacturing capacity or quality standards, this strategic approach to resource allocation helps businesses attain more financial flexibility and keep competitive advantages in fast-changing markets.
Enhanced Quality and Technical Expertise
Professional metal stamping facilities keep teams of knowledgeable engineers, metallurgists, and competent technicians specialized in several forming techniques, materials, and innovative production technologies across many sectors. These professionals have a thorough understanding of metal characteristics, tooling design, die maintenance, surface finishing methods, and precision manufacturing procedures for many uses and production needs. Their great technical knowledge helps to find possible design improvements, production efficiencies, and cost-saving possibilities all around the manufacturing lifetime as well as to enable ongoing quality optimization throughout production cycles. Modern quality control systems guarantee the exact validation of important component criteria and manufacturing parameters by use of automated inspection equipment and real-time monitoring instruments. While generating regularly reproducible results for mission-critical components, rigorous testing processes, and quality control systems maintained by specialist suppliers assist in ensuring strict adherence to industry standards, material requirements, and tight dimensional tolerances.
Increased Production Flexibility
Scalable production capabilities of external metal stamping partners allow you to fit your evolving manufacturing requirements throughout many market cycles and business situations. You may rapidly boost production levels during periods of high demand without making investments in new equipment, building facility space, or staffing to satisfy consumer needs. On the other hand, when demand declines or the state of the market changes, you free yourself from a load of unneeded capacity, extra inventory, and related overhead expenses, usually affecting internal production activities. Maintaining ideal operational efficiency across all production volumes, this natural production flexibility helps your company to react more effectively to seasonal swings, unforeseen market needs, and changing client specifications. By enabling your company to keep cost-effective operations independent of market conditions and guaranteeing constant product quality and delivery schedules, the ability to scale production up or down smoothly through outsourcing relationships offers a major competitive advantage.
Access to Advanced Technology
Leading metal stamping companies keep their competitive edge and satisfy changing market needs by always investing in cutting-edge production methods and tools. Without the large financial commitment usually necessary for in-house skills, your company immediately obtains access to modern stamping techniques, automated manufacturing equipment, and precise measuring instruments. Modern stamping operations make use of complex technological ecosystems comprising computer-aided design (CAD) software, multi-axis CNC machines, and automated quality inspection systems guaranteeing exact, repeatable outcomes throughout large-scale manufacturing runs. Advanced production planning tools, real-time monitoring systems, and predictive maintenance techniques combined for maximum manufacturing efficiency while lowering possible downtime and quality problems. Ensuring your components either meet or surpass industry standards and client needs guarantees that this complete technical edge greatly improves product quality, lowers lead times, and increases general production efficiency. Established stamping suppliers’ continuous investment in emerging technologies and Industry 4.0 capabilities guarantees that your production processes stay at the forefront of innovation without needing direct investment in fast-developing technological infrastructure.
Conclusion
The calculated choice to outsource metal stamping processes might change your manufacturing capacity and competitive posture. Your company may reach better operational efficiency, consistent quality, and more flexibility by using the knowledge, tools, and sophisticated skills of specialized suppliers; for businesses looking for sustained development and market success, working with seasoned metal-forming experts becomes ever more important as production technology keeps changing.
sources
https://www.mfg.com/blog/the-8-benefits-of-outsourcing-manufacturing
https://bhamspec.co.uk/the-benefits-of-outsourcing-your-metal-stamping