How to Choose the Right CNC Machining Service for Your Project
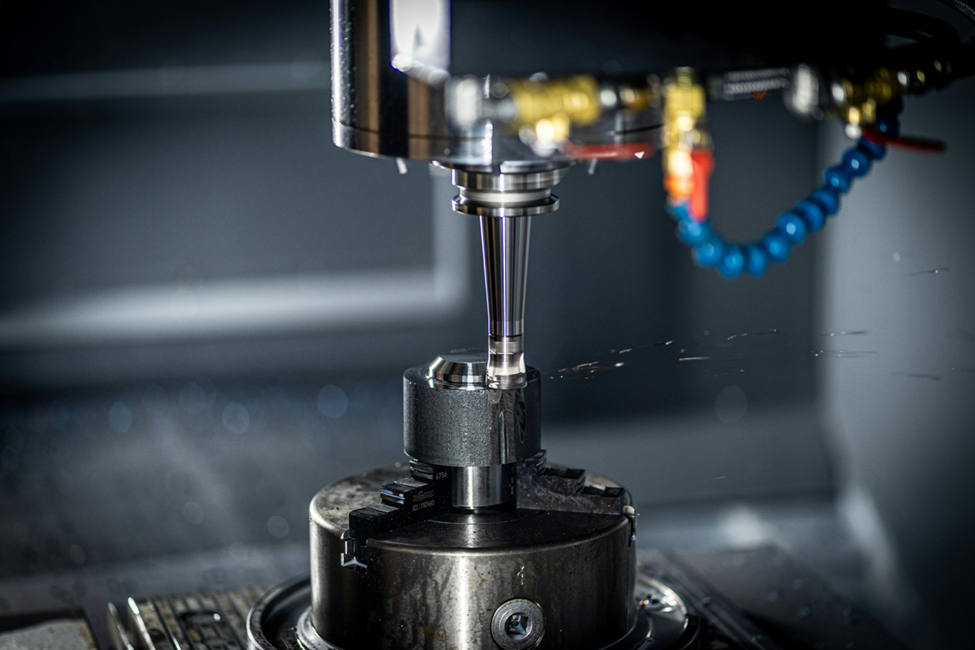
Image source: pexels
Selecting the correct manufacturing partner for precision machining may make all the difference in the success or expensive failures of a project. Whether you are designing huge production runs or prototypes, your results will be much affected by knowing the main elements of the choice process. This guide looks at the key factors to enable you to assess and choose a machining partner most suited for your production requirements.
Technical Capabilities and Equipment
Every effective CNC project starts with the technical capacity and infrastructure of the service provider. Modern production calls for very accurate, sophisticated precision tools able to manage different materials and intricate shapes. Potential partners should be assessed depending on their complete machinery characteristics, including sophisticated axis capabilities, working envelope sizes, tolerance ranges, and material processing capacity. Advanced 5-axis machines allow more complicated items to be produced in a single configuration, therefore possibly lowering operational costs and improving dimensional accuracy over several surfaces by increasing flexibility and adaptability in manufacturing. Furthermore, take into account whether the provider keeps modern systems for CAD/CAM programming, process simulation, and quality control monitoring, as these technical elements directly affect the consistency and ultimate result quality. To guarantee the best machining performance for your particular needs, the provider should also show knowledge in specialized tool selection, cutting parameters optimization, and fixture design.
Quality Control and Certification Standards
Strong quality control procedures and relentless adherence to strict industry standards over the production lifetime define manufacturing excellence most of the time. When evaluating CNC machining service providers, closely review their complete quality control methods, certifications, and history of upholding constant standards. Certified under ISO 9001, one shows a basic dedication to quality control methods and ongoing development. Industry-specific certifications like AS9100 for aerospace uses or ISO 13485 for medical device manufacture, on the other hand, show specialized knowledge and stringent regulatory compliance. Ask for comprehensive details on their quality assurance procedures, advanced measuring tools utilized, calibration schedules, and frequency of production-based quality checks. Gaining knowledge of their methodical approach to statistical process control, non-conformance management, root cause analysis, and corrective action application helps one to appreciate their long-term quality commitment better. Analyze also their investments in material certifications, documentation systems, quality control personnel training, and thorough inspection reports. Think about their First Article Inspection (FAI) experience as well as their capacity to satisfy certain industry quality criteria such as FMEA (Failure Mode and Effects Analysis) or PPAP (Production Part Approval Process). The provider’s capacity to give regularly high-quality components is much influenced by their dedication to preserving environmental circumstances, material traceability, and correct handling practices.
Project Management and Communication
Effective project management and open lines of contact are prerequisites for both successful manufacturing alliances and the seamless operation of difficult machining projects. Review how vendors manage thorough project documentation, including precise technical drawings, material standards, revision control systems, and manufacturing process plans. Think about their reaction times to technical questions, their methods of communication across several manufacturing stages, and their capacity to regularly, precisely project updates via set reporting systems. Where relevant throughout the project life, a supplier should show great knowledge in manufacturing process planning and optimization, therefore providing useful advice for design enhancements, material selection alternatives, and cost-cutting techniques. Their advanced project management system should have well-documented protocols for managing design changes or technological issues that could develop during production, resource allocation strategies, strong milestone tracking tools, and well-specified timescales. Evaluate their ability to supply technical support teams, specialized project managers, and quality assurance personnel able to collaborate across departments and stakeholders. To guarantee traceability and responsibility all through production, the supplier should record all project talks, design iterations, and process adjustments. Think about their experience running related projects for your company, their ability to scale production to demand variances, and their urgent request or accelerated order processes.
Conclusion
Selecting the correct CNC machining partner calls for a thorough assessment of several criteria outside simple capacity and cost. Thoroughly evaluating technical skills, quality processes, and project management techniques can help you choose a supplier fit for your production requirements. Before deciding, give references some time to be checked, go over some sample work, and talk about certain project criteria. Recall that the correct cooperation may enable long-term manufacturing success and support your industry’s competitiveness maintenance.
Author Bio
Hi, my name is Halley Jones. I’m a freelance content writer and guest author with a passion for crafting engaging and informative articles on a variety of topics. I have 5 years of experience in the industry and know how to create content that resonates with readers. In my spare time, you can find me hiking, trying out new recipes in the kitchen, or curled up with a good book.
sources